Optically Clear Silicone
Optically clear silicone provides excellent light transmission and long-lasting results for LED lighting manufacturers. With SMI, you have design flexibility meaning you can customize the shape, color, and light intensity of the silicone solution to best support your final product.
Benefits of Optically Clear Silicone for Lighting Applications:
Silicone UV stability provides protection from the elements making it ideal for outdoor applications and the perfect alternative to glass/plastic lighting enclosures. Plus, silicone is optically clear with 98% light transmission that won’t become yellow or brittle over time. With temperature resistance capable of enduring LED bulb heat, electrical current insulation, and crack resistance, silicone is the best way to ensure high performance and quality lighting.
SMI Lighting Expertise and Custom Lighting Solutions
Not all lighting solutions are created equal, that is why at SMI we focus on the custom solution that our lighting manufacturer partners need. We offer micromolding and overmolding for tight tolerances and compression molding. Additionally, part of SMI custom solutions is our ability to adhere silicone to other parts or materials including bonding to plastic, metal, or other silicone parts.
Some of the most common lighting applications featuring silicone include: lenses for emergency vehicles, lighting in surgical settings, close contact lighting, alternatives to plastic light enclosures, applications requiring high heat, and other critical applications that cannot allow for broken bulbs.
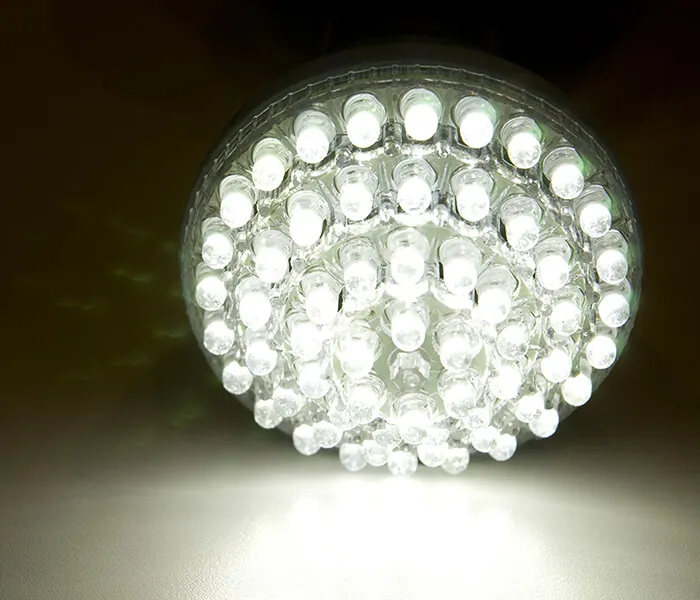
FAQ
Silicone is a highly versatile element that is widely used in many different applications and industries. However, despite its many desirable characteristics, there are some downsides to using silicone for the fabrication of LEDs. This is due to the unique properties of silicone as an indirect band gap semiconductor. Unlike more traditional direct bandgap materials like gallium arsenide, silicone cannot support the necessary electron-hole recombination required to produce light emission. Rather, this process involves the transfer of momentum as well as energy, which results in heat and light being produced together. Because of this, silicone is less suitable than other materials for the production of LED devices. Still, even with these limitations, silicone remains a popular choice for many applications where lower energy emissions or greater durability and stability are desired over higher efficiency or performance. And while it may not be ideal for use in LED technology, its many attributes continue to make it a valuable part of our modern world.
No, silicone is not an ideal choice for the fabrication of LEDs. This is because silicone is an indirect band gap semiconductor, meaning that electrons must undergo multiple energy and momentum changes before they are able to fall into the valence band. As a result, energy is released as both heat and light during this transition.